After two years of construction, Richard Crookes Constructions has transformed Walsh Bay’s Pier 2/3 from an empty wool store to a premium 21st-century space for theatre and music performance. Combined with Wharf 4/5, which was completed in 2020, this premier arts precinct will establish Sydney’s reputation as a global player in the arts sector.
Working over water on an over 100-year-old pier presented unique construction challenges for the project team to overcome. An extensive program of structural strengthening of the pier paved the way for new state-of-the-art facilities that are acoustically sound and tailored to the needs of each resident art company.

HME Services designed, supplied and installed the technical aspects to all of the venues and companies housed in Pier 2/3. These resident companies are the Australian Chamber Orchestra, Bell Shakespeare and the Australian Theatre for Young People.
The ACO’s new home at Pier 2/3 is the culmination of a dream especially as they spent the past two decades in underground premises in Circular Quay.
To increase usable space, large sections of the roof in the central valleys were raised to facilitate more room for lighting and sound equipment inside the Australian Chamber Orchestra. Retractable seating banks have been installed in the Australian Chamber Orchestra performance space to allow for multiple seating configurations for flexibility in performances.
HME Services supplied the ACO with Theatrical Drapes and Curtain Track, Removable Lighting Spigots, Technical Panels, Performance Lighting Dimmers, Removable Balcony Drapes, DMX Distribution System, Paradigm Architectural Control and Theatre Equipment.

“The ACO in particular offered some really unique engineering challenges with the level of design that was applied to their spaces,” commented Guy Gimpel, HME Service’s Project Engineer. “The acoustic and aesthetic requirements of both the auditorium and rehearsal room means that special care had to be taken with the design of elements which would otherwise be quite industrial. HME was fortunate enough to be able to work with all of the top tier trades in these rooms to come up with some elegant and robust performance systems that managed to hit both the form and functionality criteria that the job demanded and this was during the middle of the pandemic with all of the supply chain bottlenecks. Being able to distil these systems down into something that presents to a client as a simple interface within this environment has been a really rewarding experience for our team.”

ACO AUDITORIUM
Theatrical Drapes and Curtain Track
Theatrical drapes and tracks are installed within the auditorium to provide masking and the capacity to alter the venue acoustically and spatially. HME curtain tracks, designed to be used with HME curtain runners that are low noise and low friction, are installed and curtains can be travelled by hand. Stoppers have been installed in tracks where fire egress clearance needs to be maintained and where individual tracks end. In locations where drapes are fixed to motorised bars or architectural features, the drapes fix to the track or suspension system with ties or other static mounting hardware. All theatrical drapes in the Walsh Bay Arts Precinct are inherently fire retarded.
Removable Lighting Spigots
The auditorium contains sixteen removable lighting bars to provide infrastructure for performance lighting throughout the room. These removable items can be fixed in any location between balustrades along the auditorium balcony. The purpose of these bars is to provide access points for the connection of performance equipment within the space.
Motorised Lighting Bars
Lighting bars in the auditorium are hoisted using HME machinery, in this space, the EPH-800 is used. These hoisted bars double as motorised rigging bars and have a working load limit of 600kg each. The hoisted lighting bars host a total of twelve 10A circuits across the space, as well as the following other services such as Single-Mode Optical Fibre and CAT 6A Lighting Data.
The infrastructure for the lighting circuits and on-board services is managed through an HME cable bin, using an industrial-grade flexible drag chain. Operation of the motorised lighting bars is done using the handheld touch screen pendant.

Technical Panels
There are 45 technical panels to support performance equipment at designated locations around the space. The technical panels support six circuits each at stage level and one each in the balcony, all of which are hard-wired back to the dimmer system.
Performance Lighting Dimmers
Performance lighting in the auditorium is managed by a dimmer rack containing two ETC Sense3 96 channel dimmers. The dimmer racks are hard-wired and each dimmed circuit routes directly to a lighting outlet in the field. The dimmers themselves are linked and addressed via DMX over a Streaming ACN protocol. The dimmer racks have GPO outlets and can be connected in the field using a patch bay. The dimmed circuits are typically controlled via DMX from an outboard console, however, if a circuit is required to be tested it is worthwhile noting that the dimmers can operate circuits in test mode. This can be achieved by navigating through the menu on the unit.
Removable Balcony Drapes
Theauditorium contains 24 removable drapes that can be optionally mounted along the perimeter of the space. These are high fullness drapes to provide acoustic treatment for the room if required.
DMX Distribution System
The auditorium utilises four custom DMX distribution units, one in each corner of the balcony to manage performance lighting control. These splitters have been hardwired into the building system to provide live DMX outlets throughout the balcony to support any performance configuration. These distribution units and all of the other lighting infrastructure sit on a sACN backbone which permits all of the DMX outlets to run simultaneously and independently.

Paradigm Architectural Control
The Paradigm system allows the auditorium to combine architectural lighting with performance lighting functionality. This system can be accessed from touchscreens around the venue and links the auditorium with other spaces within the tenancy. When in performance mode, the lighting console will take precedence over the Paradigm System for lighting control.
Theatre Equipment
HME Services supplied 15 x ETC Source 4 Series 2 Lustr+, 18 x Selecon 7/56 degree Fresnels, 10 x Selecon PC Lighting fixtures, 12 x Chroma-Q ColorForce 72 cyc battens, 40 x ETC Source 4 Zooms of various degrees and for control, an ETC Ion XE console. A selection of lighting accessories was also supplied.
“The performance infrastructure within the ACO auditorium is one of the more service-heavy designs HME have done over the years, with each flown lighting bar supporting more services than most university lecture theatres,” added Guy Gimpel. “Concealing all of the services to present a slick and minimal piece of rigging equipment was no small feat and the level of coordination that went into making sure all of our equipment could interface well with the other trades was substantial. The outcome of this work has provided a series of highly functional locations for the connection of technology and equipment to turn the architecturally beautiful space into a state of the art performance venue that facilitates cutting edge hardware within a traditional timber room.”
ACO REHEARSAL ROOM
HME Services also took care of the ACO Rehearsal Room supplying drapes and motorised curtain tracks. The curtain motors use an outboard controller to allow user management of the theatrical drapes. The control system uses tactile push buttons and has programmed latching to allow the curtains to run across to their limits without the need for dead-man style switch operation.
The rehearsal room contains thirteen technical panels to support performance equipment at designated locations around the space. Ten of the thirteen panels are located in the ceiling, at access panel locations, whilst the other three are located at stage level. All of the technical panels in the rehearsal room use Socapex connectors.
Performance lighting in the rehearsal room is managed by a dimmer rack containing three LSC 12 channel dimmers. The dimmer racks are mobile, with an 84 tail Redback Patch Bay providing tails routed directly to lighting outlets in the field. The dimmers themselves are linked and addressed via DMX. The Redback Patch Bay also houses a hot patch unit, which provides general power if an outlet in the field needs to be tested before being connected to the dimmer system. This can be a useful tool for fault-finding.
ACO Rehearsal uses eight lighting tee bars installed in the ceiling to allow the suspension of ROBE Robin LEDBeam 350 intelligent lights. Also supplied are 12 x ETC Source 4 Series 2 Lustr+, 12 x ETC Tungsten Profiles, 16 x Selecon 1200w Fresnels and an ETC Colorsource 40 control console.
ACO FUNCTION SPACE
ACO Function Space contains twelve static rigging points installed throughout the space to provide locations for suspended equipment or assisted lifting.
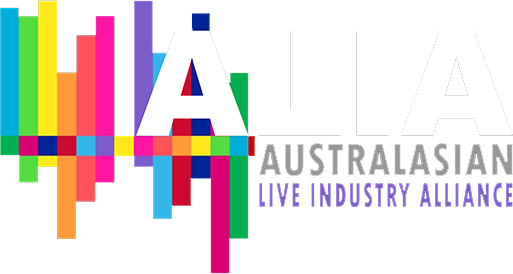