Data Strategy’s QC-Check workstation is globally relied upon in the production industry, for quality assurance and peace of mind. One of Australia’s biggest production suppliers, Creative Technology Australia and New Zealand, opted for QC-Check to address three main needs in terms of product inspection: socapex cable testing, the safe inspection of twin-frame distribution boards, and the ability to set up the specific testing processes needed to be carried out by anyone in the warehouse.
Maintenance manager, Myles Barlow, explained that the company’s highest priority was to be able to test multipin connectors such as Socapex three-phase cables, as “…there’s just no safe way to test them.”
In addition, he found that “…standard pat testers fail products that have lots of internal relay, control voltages and several limit points. They see it as a dead short when there’s actually not a problem.” So without, QC-Check there was no effective way of PAT testing products like twin-frame distribution boards or other items with ‘smarts’ in them.
Custom engineered by SES Entertainment services in the UK, Creative Technology’s QC-Check workstation was custom designed to test the various types of connectors used by the Australian production house on a day-to-day basis. The main body of QC-Check housed the larger connectors, whilst the smaller and more regularly tested connectors were situated on the workstation bridge.
Alongside industry standard connectors like tru-con, neutrik and powercon connections, Creative Technology’s two-bay QC-Check featured standard Australian 240volt sockets, and 32 amp three-phase test connections specific to Australia, known as ‘Wilco’s’.
QC-Check, shipped to Melbourne and commissioned remotely from the UK by Data Strategy MD, Iain Roche, has proven a hit with Creative Technology Australia and New Zealand. “It covers everything we have now and everything we’d buy in the future,” Myles proudly confirms. “Plus, testing a whole socapex that might have taken me five to six minutes, can be tested now in under a minute. I bought three kilometres of socapex cable last week.”
Data Strategy’s QC-Check system links to and interacts with production hire software, which for Creative Technology Australia and New Zealand is R2. The system maintains a fully logged, QC-tested environment where all products are automatically and regularly tested as part of the company’s existing operational workflow, using Out Board’s industrial PAT-4 / CAB-5 Cable Testers.
Now, each product in the warehouse is individually identifiable by its bar code and grouped with its own test definitions by product. Whilst bar-coding products using the custom print facility within QC-Check, Creative Technology took the opportunity to add the company logo to its labels. “Now we brand our cables,” Myles explains. “No other company here does that and we find there’s less chance of people nicking them!”
One of the greatest benefits that Myles has seen, however, is the simplicity of testing using the QC-Check. With testing processes created in QC-Check by a ‘competent person’, electrical testing can be carried out by any other person deemed competent, and as Myles explains, “It’s quite straightforward to carry out the tests because you set it up with lots of triggers along the line telling you what to do. It’s simple to follow but also you set it up to test exactly what needs testing. Unlike generic testers, you’re not locked into the tests they think you want.”
For large-scale production companies and corporate AV production, Data strategy’s QC-check is an essential part of the warehousing process and Myles believes, “A lot of companies could now see it as a valuable investment over here in the Asia Pacific region.”
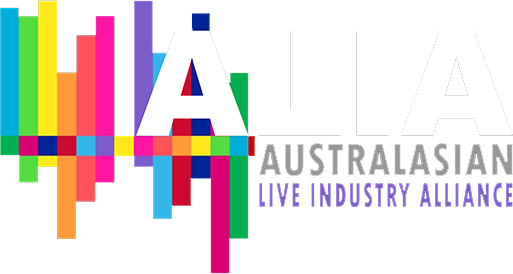